[20
OCT 98] JAGUAR PRESS RELEASE
The New S-Type At A GlancePROCESS
- S-TYPE was designed and developed through innovative process management including early
component sourcing, crossfunctional programme teams, advanced quality planning, rapid
prototyping and predictive/analytical techniques.
- Dynamic Programme Simulation provided a rigorous, computer-based analytical 'test bed'
to determine, in advance, the implications of management decisions on issues such as
resources, productivity and prototype scheduling - the first automotive application of
this technique.
- Dimensional Management, employing computer-based assembly variation modelling
techniques, was used to determine the optimum body design, before building any prototypes.
Over one million 'virtual' cars were built on the computer to establish optimal assembly
processes before the start of production.
- Intensive operator training programmes and the building of prototypes on the production
line helped ensure manufacturing readiness at launch
- More than 450 prototype and pre-production AJ-V6 engines were built and tested on
dynamometers and in vehicles.
- Simulated autobahn durability tests were conducted equivalent to 100,000 miles at an
average of over 100 mph.
- Body engineers undertook computer aided simulation and aluminium soft tooling techniques
to perfect panel radii, material flow and manufacturing of the two-pressing, highly styled
bonnet assembly.
- Extensive acoustic windtunnel testing ensured best-in-class 'windnoise' isolation.
BODY STRUCTURE
- 'Limousine'-style door design extends into the roof line for easier entry and exit
- One-piece body side, incorporating the rear wing and a one-piece front door opening
panel provides a highly stable structure ensuring highly consistent shut lines and door
seal location.
- A plastic moulded reinforcement member, highly complex in shape, provides a very stable
mounting for the style-critical headlamps and grille.
- Leading-edge hydroform technology, injecting oil into a tube of steel, was used to mould
the shape of the complex radiator crossmember
- High strength steel was used in critical areas of the body following extensive finite
element analysis, optimising the weight of the bodyshell.
- All doors have triple seals with welded locating channels for optimum refinement.
- Body apertures restricted to a total of 25 cm2 to minimise air leakage,
maximising perceived refinement.
- 85 per cent of body-in-white, including all vulnerable areas, are double-sided, zinc
coated steel
- Specially shaped plastic outer sills minimise risk of stone chips on bottoms of doors.
EXTERIOR FEATURES
- One-piece body coloured front/rear bumpers with energy absorbing moulded polypropylene
foam core resist parking knocks at up to 5mph (8 Km/h).
- Front grille, integral with front bumper, moves backwards in minor accidents without
damaging adjacent components.
- Front bumper incorporates foglamps and telescopic headlamp power wash, where specified.
- Fine-wire heated wiper park fitted as standard to front screen (full heated screen is an
option).
- Rear screen contains antennae for audio, security, cellular phone and Trafficmaster,
where specified.
- Elliptical quad headlamps have impact resistant polycarbonate lenses and use 'freeform'
reflectors with a high gloss, aluminium, vacuum metallised finish for jewel-like
appearance. All lamps have long-life bulbs.
- Electronic headlamp levelling and automatically operating headlamps, responding to
ambient light, are standard.
- Reverse Park Control, incorporating rear bumper mounted sensors and audible warning is
available as an option.
- Rain Sensitive Wipers, working on the principle of refracted light using photodiodes and
light-emitting diodes, are optional fit.
- A glass sunroof with electrically operated tilt/slide and encapsulated seal is standard.
INTERIOR STYLE AND ENGINEERING
- Soft-feel foam and slush moulded facia skin over a rigid injection moulded armature has
an integrally moulded passenger airbag deployment door for a tamper-proof, perfect fit.
- Strong tubular steel crossbeam fits behind the facia, enhancing refinement through
torsional rigidity and crash performance, while providing very stable mounting for the
steering column, minimising vibration.
- Five-function trip computer with two independent memories is integral with the
instrument pack and VF, eleven language message centre display.
- Ignition key barrel ergonomically located in the facia
- Mirror polished, Mushroom stained bird's eye maple veneers on doors, facia and console.
One-piece, full width facia veneer employs a light weight magnesium substrate for enhanced
quality and durability.
- 8-way electrically adjustable front seats are standard on 3.0 V6 with a 2-position
memory recall facility (seats, steering column and exterior mirrors) available as an
option on 3.0 V6 and as standard on 3.0 V6 'special equipment' and 4.0 V8.
- Steering column adjustable for tilt and reach is standard, electrically operated on 3.0
V6 'special equipment' and 4.0 V8.
- Front seats incorporate side airbags to protect both head and chest.
- Bench-style rear seat with, for the first time in a Jaguar, a 60/40 folding backrest.
- All five seating positions have adjustable head restraints.
- Optional, electrically operated 'scissor action rear sunblind.
- Optional facia-mounted phone presenter.
- Multi-function luggage retention system, including four tie-down points, in the boot.
- Steering wheel controls for main audio, telephone and cruise control functions is
standard on 3.0 V6 special equipment' and 4.0 V8 (optional on 3.0 V6) for safe,
hands-free operation.
- Electrically adjustable, heated door mirrors are standard with a power fold back option.
- Optional electrochromic interior mirror.
- Automatic climate control system - Jaguar's first dual-zone system - with particle
filtration, is standard fitment on all models. 4.0 V8 models have a residual heating
system providing heat to the cabin at low ambients for up to 20 minutes after the engine
is switched off.
POWERTRAIN
- New 240bhp DIN (1 79 kW) 60O, all-aluminium quad cam 3.0 litre AJ-V6 -
Jaguar's first ever production V6 - delivers best-in-class specific power of 80.9
bhp/litre (60.3kW/litre) with 90 per cent of peak torque available between 2500 and 6000
rev/min.
- AJ-V6 shares design features with 4.0 AJ-V8 including combustion and low volume
cooling systems, cylinder head and valvegear.
- AJ-V6 'first-for-Jaguar' features include 3-stage, variable intake manifold with
dual-intake tuning valves and long, equal length exhaust downpipes for maximum low speed
torque.
- Proven, 280 bhp DIN (209 kW) all-aluminium, quad cam 4.0 litre AJ-V8 now features linear
variable cam phasing, full authority throttle body, air assist injection and twin-wall
exhaust manifolds.
- Lightweight 5-speed Getrag manual transmission available with AJ-V6 engine.
- New 5-speed automatic transmission - standard on 4.0 V8 and 3.0 V6 'special equipment' -
features wide ratio spread for optimum performance, economy and refinement and fully
electronic, intelligent gearshift control.
- Bespoke powertrain electronic controller which integrates both engine and transmission
functions, has a memory capacity of 1 Megabyte.
VEHICLE DYNAMICS
- All-independent, double wishbone front and rear suspension with extensive use of light
weight aluminium componentry and twin front crossbeams.
- Variable ratio, speed proportional power steering.
- Ventilated discs front and rear and 4 channel antilock with electronic brake
distribution for enhanced stability in adverse conditions.
- Standard-fit electronic traction control system with engine and brake intervention.
- Optional electronic Dynamic Stability Control system linking with the anti-lock,
traction control and steering systems to prevent oversteer.
- Optional Computer Active Technology Suspension (CATS), employing two-stage electronic
adaptive dampers.
- Pirelli P6000 (16 inch) and P Zero (1 7 inch) tyre systems.
- Ideal 50/50 front/rear weight distribution.
ELECTRONICS
- Single multiplexed network links all major powertrain, chassis and body electronic
control modules, transmitting data at up to 700 messages per second. Fewer, shorter wires
improve packaging quality and reliability.
- Engine and transmission control is achieved by a single module with a dedicated, high
speed internal communication link. This powertrain controller connects by hard wire for
high speed communication to the throttle body to operate the full authority electronic
throttle.
- A combined electronic module for anti-lock brakes, traction control and steering systems
provides full chassis systems integration.
SECURITY SYSTEMS
- RF remote controlled security systems, fully integrated into the vehicle's electronics
system exceed insurance industry criteria and include perimeter alarm and immobiliser with
random encrypted coding, deadlocking, volumetric intrusion sensing, automatic locking on
drive-away and 'smart' locking, helping to prevent locking the key inside the car.
- Fully encrypted, electromechanical steering column lock responds only to dedicated
transponder key. Steering column locking mechanism is integrated into facia, preventing
physical attack.
- Global open/close for windows and sunroof.
AUDIO, COMMUNICATIONS AND TELEMATICS SYSTEMS
- For the first time on a production car, optional voice activated controls for the audio
(radio/cassette/CD), phone and climate control systems, responding to the spoken
instructions of the driver, provide safe, hands-free operation. The system responds to a
wide diversity of English and North American accents, but also provides for training to
recognise a specific voice.
- A first for Jaguar is the optional fully integrated, onboard satellite navigation system
using multi-lingual, digitised map data on CD-ROM. The system can point out useful
landmarks and points of interest and links with the UK's Trafficmaster system to provide
real time data on traffic delays.
- The 175 Watt, twelve speaker, premium sound system, features two active "centre
fill' speakers, an active sub-woofer enclosure and 6-disc C.D. autochanger. Digital sound
processing, working with Dolby, provides special audio effects and compensates for the
number of vehicle occupants.
- The premium specification Motorola Startac 130 portable GSM phone is a factory fit
option, combining the advantages of vehicle integration, safety, convenience and
performance with the versatility of a pocket phone.
SAFETY / ENVIRONMENT
- Bodyshell exceeds all crash legislation worldwide, including the latest European side
impact and offset frontal impact tests.
- Computer analysis and modelling were used extensively by engineers together with a
comprehensive dynamic crash test programme.
- High strength steel used in critical areas such as front longitudinals, seat belt
anchorages and suspension mounting points.
- Doors have hot-stamped boron steel side intrusion beams, full height B/C post and A
pillar reinforcements and one-piece front and rear door hinge reinforcement panels, all in
high strength steel.
- 'Catcher' bracket assemblies retain rear doors in their frames in the event of side
impact.
- Front end structure dissipates crash energy efficiently via convoluted front rails and a
roll formed solid steel beam.
- Energy absorbing ribs, moulded into the upper A and B/C pillar trim panels, and a
headliner of energy absorbing foam reduce risk of head injury.
- Fuel system includes deformable, plastic fuel tank under the rear floor, away from
impact zones and an inertia fuel cut-off switch.
- Front seat-mounted, side airbags protect both head and ribcage.
- Twin frontal airbags and pyrotechnic seatbelt pretensioners; passenger bag is powered by
environmentally friendly mix of clean air and twelve per cent hydrogen, which is smokeless
and easier to recycle.
- All rear seating positions have three point belts with automatically locking retractors,
ensuring child seats are securely restrained.
- Leading-edge restraints control module can discriminate between crash events warranting
airbag deployment and those which don't.
- Internally stroked steering column which telescopes within its own length, combines with
stiff mounts to achieve very robust and repeatable crash 'stroke'.
- AJ-V6 and AJ-V8 engines meet toughest exhaust and evaporative emission standards in the
world. High compression ratios, fast warm-up precision cooling system, variable cam
phasing and twin close-coupled catalysts deliver low emissions and good fuel economy.
- A minimum of 80 per cent by weight of each S-TYPE is recyclable, while 84 per cent of
component packaging is durable and returnable.
MANUFACTURING
- Development of Jaguar's Castle Bromwich site is one of the largest UK inner city
investments for 50 years.
- At Castle Bromwich, S-TYPE bodies are constructed, painted and finally assembled into
complete cars (on the same site, the bodies for Jaguar XJ saloon and XK sports cars are
constructed, painted and shipped to Jaguar's Browns Lane plant in Coventry for final
assembly).
- The majority of components are delivered by suppliers to the trackside on a just-in-time
basis.
- 4500 spot welds on each S-TYPE body are applied by the latest computer controlled
machines, using closed-loop secondary current control for precision welding.
- Body panels may be audited by positioning in environmental cubes which
perform a thorough geometric check of all components.
- The one-piece body side pressings, incorporating the rear wing, nearly 4 metres long,
are formed in a 2,000 tonne capacity press.
- Door and bonnet outer panels are made from a special bake-hardening steel, more
resistant to minor impacts.
- Accurate fitting of doors, bonnet and bootlid ensured by precise measurement of body
openings, achieved by means of a laser camera system, which also performs a final check on
the overall geometry of the body.
- Paint shop is a sealed, clean room with controlled temperature and humidity. Among the
environmental measures are close control and incineration of remaining paint solvent
emissions.
- New environmentally efficient, gas-fired boiler house and effluent treatment facility
installed at Castle Bromwich for S-TYPE production.
- Waterborne paint system cuts basecoat solvent emissions by 85 per cent.
- The body is internally protected by hot wax injection, which flows into place during
stoving.
- Final assembly is performed on a series of skillets (platforms of laminated wood) to
create a continuously moving floor for efficient, ergonomic assembly.
- The drivetrain is built up in two separate assemblies:
(i) engine, transmission, front suspension, brakes and steering rear axle assembly -
(ii) final drive, rear drive shafts, rear suspension and brakes.
- With the addition of the propeller shaft the complete driveline assembly is dynamically
balanced in a special rig, rotating the propshaft at 250Orev/min.
- When mating the driveline to the body, laser cameras are used to validate alignment.
- Each completed car is the subject of a comprehensive electrical check by means of VCATS
(Vehicle Configuration and Test Systems).
- Non-contact laser technology measures front and rear suspension geometry and headlamp
alignment.
- Further validation is performed on a rolling road, including engine, transmission,
brakes.
- At the final inspection stage, each car passes through a high intensity water spray
line, equivalent of a monsoon, tilting the car to simulate 'awkward' parking situations.
All water test facilities feature a low loss recirculation system.
|
|
 |







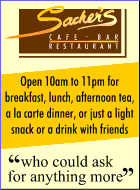

|